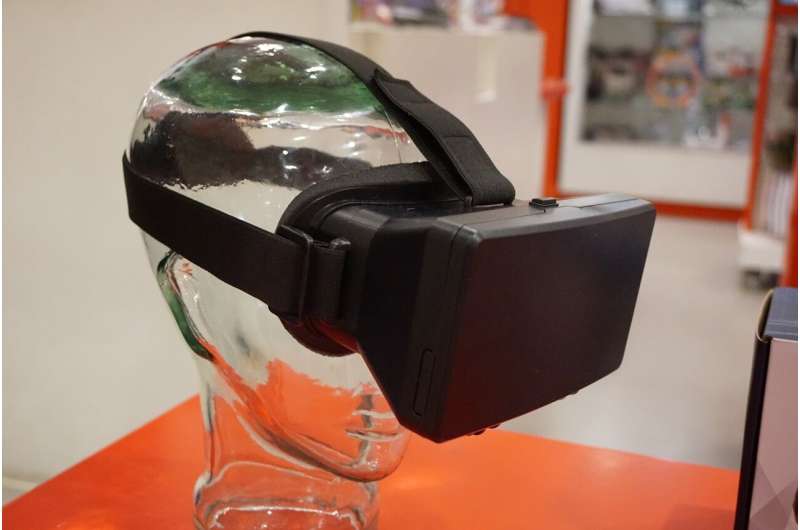
인공 지능 기반 사진 검사, 3D 프린팅 도구 및 증강 현실 훈련 헤드셋은 차량 품질을 향상하려는 Ford Motor Co.의 전략의 일부이며, 이는 계속해서 재무 결과를 괴롭혀 왔습니다.
2분기 Dearborn 자동차 제조업체는 2021년 이전 차량에 대한 보증 비용이 예기치 않게 급증한 후 순이익이 전년 동기 대비 5% 이상 감소했다는 비난을 받았습니다.이러한 타격은 회사가 새로운 리더십, 개선된 제조 시스템 및 첨단 기술을 통해 해결하려고 노력해 온 핵심 영역인 자동차의 낮은 품질 결과로 인해 수년간 부정적인 재정적 영향을 받은 데 따른 것입니다.
느린 차량 출시 및 램프업 프로세스로 인해 회사는 비용을 지출하고 있습니다. 작년에 Super Duty 출시에 대한 새로운 절차로 인해 Ford는 약 10억 달러의 비용을 지출했습니다.그러나 포드 경영진은 더 나은 결과를 얻을 수 있는 가치가 있으며 새로운 산업 시스템 하에서 제품을 출시할 때마다 프로세스가 더욱 원활해지고 비용도 절감된다고 말합니다.이 브랜드는 J.D. Power의 2024년 미국 초기 품질 연구에서 23위에서 9위로 14계단 뛰어올랐습니다.
J.D.파워(J.D. Power)의 자동차 벤치마킹 수석 이사인 프랭크 핸리(Frank Hanley)는 "완전 시장 브랜드가 이렇게 큰 변화를 이루는 것은 의미가 있다"고 말했지만, 현대차도 17위에서 14계단 뛰어 올라 3위로 올라섰다고 언급했다.
"가장 큰 것은 품질에 대한 조직의 헌신입니다. 변화를 약속할 때 디자인, 제품 계획, 제조 시설 등 조직 전체가 개선을 위해 참여해야 합니다."
보다 심층적인 품질 검사, 문제를 보다 신속하게 해결하기 위한 의사소통 흐름 개선, 구매 접근 방식 개혁 등이 Ford의 노력의 일부입니다.
Hanley는 품질에 대한 회사의 헌신과 성공에 필요한 문화를 주입하려는 결단력을 나타내는 물리적 징후를 지적합니다.Ford가 구현하고 있는 도구에는 직원 교육 및 기술 향상, 직원에게 업무를 보다 효율적으로 수행할 수 있는 리소스 제공, 차량이나 부품이 다음 스테이션으로 이동하기 전에 문제를 식별하는 도구가 포함됩니다.
AI 카메라
한 가지 예는 모바일 인공 지능 비전 시스템(MAIVS)의 구현입니다.Ford 엔지니어들은 스마트폰에 장착된 카메라와 인공 지능 기술을 사용하여 Ford 소프트웨어와 통신하고 부품 키트 등의 이미지를 캡처하는 시스템을 구현했습니다.이 기술은 이미지 라이브러리와 비교하여 사진을 확인하여 어셈블리가 올바른지 확인합니다.그렇지 않은 경우 부품 키트는 수리될 때까지 스테이션에서 정지됩니다.
MAIVS는 전 세계적으로 약 20개 공장에 300개 이상의 스테이션을 보유하고 있으며 지난해 6천만 건 이상의 검사를 실시했습니다.Sterling Heights에 있는 Van Dyke Electric Powertrain Center는 운영에 이 기술을 통합한 최초의 파워트레인 공장이었습니다.
Escape, Maverick 및 Transit뿐만 아니라 순수 전기 F-150 Lightning 및 E-Transit과 같은 차량용 변속기와 전자 모터를 생산하는 이 공장에는 MAIVS가 장착된 약 10개의 스테이션이 있습니다.
한 가지 용도로 시스템은 하이브리드 자동차 모터를 냉각시키는 전기 오일 펌프의 둥근 고무 씰인 스퀴시 튜브를 평가합니다.2023년에는 월 평균 35개의 펌프에 변속기에 들어가는 스퀴시 튜브 결함이 있었고, 그 해 6월에는 불량품이 63개로 사상 최고치를 기록했습니다.올해 1월 MAIVS를 설치한 후 거부 건수는 12월 26건에서 1월 17건, 2월 13건, 3월에는 0건으로 감소해 봄, 여름 내내 그 수준을 유지했다.
Van Dyke의 품질 관리자인 Hayley Garnham은 "이러한 많은 도구와 구현을 사용하면 해당 스테이션에서 문제가 있는 부분을 차단하여 문제 부분이 발생하지 않도록 할 수 있습니다."라고 말했습니다.앞으로 넘어갈게."
3D 프린팅
또한 Van Dyke 및 기타 공장에서 Ford는 작업자가 작업을 쉽게 하고 부품을 정리하고 쉽게 접근할 수 있도록 하는 데 사용할 수 있는 3D 인쇄 도구에 적층 제조를 활용하고 있습니다.이는 올바른 부품을 사용하여 일관된 방식으로 작업을 보다 효율적으로 수행하는 데 도움이 된다고 공장 관리자인 Mark Shkoukani는 말했습니다.
Van Dyke 공장에만 두 대의 대형 3D 프린터가 있고 한 대는 주로 하루 24시간 작동하는 프로토타입용 소형 프린터라고 수석 프로세스 엔지니어인 Bill Colwell이 말했습니다.프린팅은 도구의 크기에 따라 20분에서 몇 시간까지 걸릴 수 있습니다.일반적으로 대기열에는 6개의 프로젝트가 있으며 작업자는 매일 아이디어를 가지고 접근합니다.
라인에서 일하는 직원이 도구에 대한 아이디어가 있으면 Colwell이나 그의 동료 중 한 명에게 올 수 있습니다.그들은 함께 디자인을 스케치하고 Colwell은 이를 사용하여 일반적으로 플라스틱을 사용하여 3D 프린터가 생산할 수 있는 디자인을 만듭니다.Ford가 공급업체를 거쳐야 했던 과거에 비해 이 프로세스는 하루 안에 운영자의 손에 도구를 제공할 수 있으며, 추가 조정이 필요한 경우 몇 주 또는 몇 달이 걸릴 수 있습니다.
Colwell은 "우리는 몇 시간 내에 무언가를 구현하고 시도해 볼 수 있으며 작동하지 않으면 바로 돌아가서 이미 가지고 있던 것과 동일한 모델을 가져와 즉시 인쇄하고 약간만 변경할 수 있습니다"라고 말했습니다.그것에."
Van Dyke 공장의 United Auto Workers 팀 리더이자 Mount Clemens의 Chris Kipp(52세)은 엔지니어와 협력하여 작업자가 전기 구동 장치의 부품인 로터의 엔드 캡을 제자리에 쉽게 밀어 넣을 수 있는 도구를 설계했습니다..원래 사용했던 도구는 부품을 아래로 누르는 데 많은 힘이 필요했습니다.
Kipp과 엔지니어들은 부품의 외부 직경이 아닌 내부 직경을 활용하는 도구를 제작함으로써 캡을 제자리에 고정하는 데 더 적은 힘이 필요한 안정성을 제공한다는 사실을 발견했습니다.그 결과, 소요 시간이 상당히 다양하고 완료하는 데 2분 이상 걸릴 수 있는 작업이 덜 가변적이 되어 80초 이내에 완료되었습니다.
"훨씬 쉬워졌습니다." Kipp이 말했습니다."운영자들은 정말 그것을 어깨에 짊어지고 있었습니다."
최근 아침 Van Dyke 공장의 조립 작업자인 Sterling Heights의 Tyler Amodeo(30세)는 여러 3D 도구를 사용하여 작업을 수행하고 있었습니다.웨이브 스프링용 홀더 하나를 사용하면 엉키지 않고 크고 얇은 와셔를 빠르게 잡을 수 있습니다.그는 파워트레인 라인으로 보내질 때 팔레트의 구성 요소를 체계적으로 유지하는 3D 프린팅 키트에 여러 부품을 넣었습니다.
Amodeo는 "조직화되고 효율적이며 빠르게 작업하는 데 도움이 됩니다."라고 말했습니다.
Shkoukani는 직원들이 필요한 도구나 부품이 없을 때 올바른 부품을 찾아 올바른 부품을 확보하는 데 시간을 투자해야 하기 때문에 이것이 핵심이라고 Shkoukani는 말했습니다.
"당신은 몇 발자국을 제거합니다"라고 그는 말했습니다."라인 아래의 여러 역에서 그렇게 하면 계산만 하면 됩니다. 시간이 너무 많이 걸리죠. 엄청난 비용 절감 효과가 있을 뿐입니다."
AR 훈련
Downriver로 향하는 Dearborn Engine은 또한 2세대 모델 소매가 3,500달러부터 시작하는 Microsoft HoloLens를 통해 직원 교육을 강화하여 긍정적인 품질 결과를 얻기 위한 노력의 일환으로 기술을 구현했습니다.
공장에서는 서면 지침, 작업을 수행하는 다른 사람의 관찰, 화면상의 3D 모델과 함께 증강 현실 고글을 교육 커리큘럼에 통합했습니다.조지아 공과대학(Georgia Institute of Technology)과의 공동 연구에 따르면 혼합 현실 단계가 근육 기억에 도움이 되는 것으로 나타났습니다. 공장 관리자인 Nadeem Zaidi는 말했습니다.
이는 특히 중요합니다. 왜냐하면 Ford는 대량 제조업체로서 강점을 갖고 있지만 Dearborn 공장은 2021년 생산이 재개될 때 재편성한 이후 더 많은 틈새 파워트레인 라인을 추가했기 때문이라고 Zaidi는 말했습니다. 결과적으로 해당 라인에서 생산되는 엔진은 거의 없습니다.이는 직업이 제2의 천성이 되는 데 더 오랜 시간이 걸린다는 것을 의미합니다.
또한 공장에서는 조립부터 기계 가공까지 한 번도 해본 적이 없는 작업에 대해 더 많은 직원을 교육하기 위해 노력하고 있다고 Zaidi는 말했습니다. "작업에 참석하는 사람들에 따라 인력을 분배하는 데 도움이 됩니다."
그는 HoloLens가 이러한 프로세스를 쉽게 만드는 데 도움이 되기를 희망한다고 말했습니다.헤드셋을 착용한 훈련생은 예를 들어 F-150 Raptor R V-8 엔진을 검사하는 방법을 설명할 수 있는 단계별 팝업 지침을 받습니다.가상의 선은 사용자에게 어디를 봐야 할지 안내하고, 사용자는 지시에 따라 따르거나 특정 지점에 가만히 머물도록 할 수 있습니다.
출시 코디네이터인 알 피셔(Al Fisher)는 "내 관점에서 가장 큰 자산은 복잡한 작업이 필요하고 아주 작은 단계로 나누어서 프로세스를 따르면 끝까지 도달할 수 있다는 것"이라고 말했습니다."때때로 전문가는 자신이 얼마나 뛰어난지 당연하게 여길 수 있습니다. 하지만 그런 것은 아닙니다. 체계적으로 단계별로 안내해 줄 것입니다."
이는 특정 분야에 대한 작업자의 전문 지식이 제한적인 경우에 도움이 될 수 있습니다.한때 공장에는 지시 없이 특정 I-4 엔진을 검사할 수 있는 전문가가 한 명 있었습니다.
Ford Production Systems 코치인 Tim Mwenje는 "만약 해당 전문가가 공장에 없다면...검사를 완료하기 위해 안간힘을 쓰는 셈입니다."라고 말했습니다."네가 이걸 입으면 나도 검사할 수 있을 것 같아."
Dearborn Engine의 직원 20명 이상이 HoloLens를 사용하여 교육을 받았으며, Ford는 지난 7월 각 구성원이 기술 교육을 받은 단일 팀의 성과를 추적하기 시작했습니다.이 응용 프로그램은 Dearborn Truck Assembly Plant, Ypsilanti의 Rawsonville Components Plant, Kentucky의 Louisville Assembly Plant를 비롯한 다른 지역에서도 확장되고 탐구되고 있습니다.
Dearborn Engine의 팀 리더이자 Redford Township에 거주하는 Reginald Bassett(42세)는 "내가 18세에 막 시작했을 때 이런 기능이 있었더라면 좋았을 것입니다"라고 말했습니다."나는 매우 시각적인 사람이기 때문에 꽤 멋지다."
2024 디트로이트뉴스.com.Tribune Content Agency, LLC에서 배포합니다.
소환:Ford가 AI, 증강 현실, 3D 프린팅을 사용하여 품질을 개선하는 방법(2024년 9월 11일)2024년 9월 11일에 확인함https://techxplore.com/news/2024-09-ford-ai-augmented-reality-3d.html에서
이 문서는 저작권의 보호를 받습니다.사적인 학습이나 조사를 목적으로 하는 공정한 거래를 제외하고는 어떠한 행위도 허용되지 않습니다.서면 허가 없이 일부를 복제할 수 있습니다.콘텐츠는 정보 제공 목적으로만 제공됩니다.