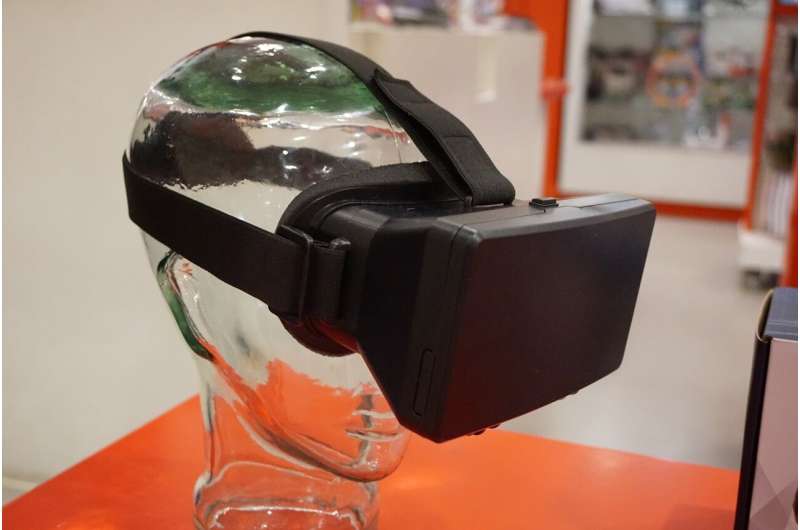
Inspecciones fotográficas impulsadas por inteligencia artificial, herramientas impresas en 3D y auriculares de entrenamiento con realidad aumentada son parte de la estrategia de Ford Motor Co. para mejorar la calidad de los vehículos, algo que ha seguido afectando sus resultados financieros.
En el segundo trimestre, el fabricante de automóviles de Dearborn se vio afectado por una disminución interanual de más del 5% en los ingresos netos después de que los costos de garantía de los vehículos anteriores a 2021 se dispararan inesperadamente.El golpe se produce después de años de efectos financieros negativos debido a resultados de mala calidad en sus vehículos, un área clave que la compañía ha estado tratando de abordar con un nuevo liderazgo, sistemas de fabricación renovados y tecnología avanzada.
Los procesos más lentos de lanzamiento y aceleración de vehículos le están costando a la compañía: los nuevos procedimientos en el lanzamiento de la Super Duty el año pasado le costaron a Ford alrededor de mil millones de dólares.Pero los ejecutivos de Ford dicen que valdrá la pena para obtener mejores resultados y que con cada lanzamiento bajo su nuevo sistema industrial, el proceso se vuelve más fluido y menos costoso.La marca saltó 14 puestos en el Estudio de calidad inicial de EE. UU. de 2024 de J.D. Power, pasando del puesto 23 al puesto 9.
"Ver una marca de mercado completo hacer un cambio tan grande como ese es significativo", dijo Frank Hanley, director senior de evaluación comparativa de automóviles de J.D. Power, aunque señaló que Hyundai también saltó 14 espacios al puesto 3 desde el 17.
"Lo más importante es el compromiso de la organización con la calidad. Cuando se comprometen con los cambios que van a realizar, tienen que contar con toda esta organización (el diseño, la planificación del producto, las instalaciones de fabricación) y todos deben participar para mejorar".
Controles de calidad más profundos, mejorar el flujo de comunicación para abordar los problemas más rápidamente y reformar su enfoque de compras son parte de ese esfuerzo en Ford.
Hanley señala indicios físicos del compromiso de la empresa con la calidad y su determinación de inculcar la cultura necesaria para tener éxito.Las herramientas que Ford está implementando incluyen aquellas que, según el fabricante de automóviles, capacitan mejor y mejoran las habilidades de los trabajadores, brindan a los empleados los recursos para hacer su trabajo de manera más eficiente e identifican problemas antes de que un vehículo o pieza pase a su siguiente estación.
cámaras de inteligencia artificial
Un ejemplo es la implementación del Sistema Móvil de Visión con Inteligencia Artificial (MAIVS).Utilizando cámaras que se encuentran en los teléfonos inteligentes y tecnología de inteligencia artificial disponible, los ingenieros de Ford implementaron el sistema para comunicarse con el software de Ford y capturar imágenes de, por ejemplo, un kit de piezas.La tecnología compara las fotografías con una biblioteca de imágenes para determinar si el ensamblaje es correcto.Si no es así, el kit de piezas se detiene en la estación hasta que se arregle.
Alrededor de 20 plantas en todo el mundo tienen más de 300 estaciones instaladas con MAIVS y realizaron más de 60 millones de inspecciones el año pasado.Van Dyke Electric Powertrain Center en Sterling Heights fue la primera planta de tren motriz en incorporar la tecnología en sus operaciones.
La planta, que produce transmisiones y motores eléctricos para vehículos como Escape, Maverick y Transit, así como los totalmente eléctricos F-150 Lightning y E-Transit, tiene aproximadamente 10 estaciones equipadas con MAIVS.
En un uso, el sistema evalúa los tubos de compresión, que son sellos de goma redondos en bombas de aceite eléctricas que enfrían los motores de vehículos híbridos.En 2023, un promedio de 35 bombas por mes tenían defectos en los tubos de aplastamiento que iban a las transmisiones, y hubo un máximo histórico de 63 rechazos en junio de ese año.Después de instalar MAIVS en enero, el número de rechazos cayó de 26 en diciembre a 17 en enero, 13 en febrero y cero en marzo, donde permaneció durante la primavera y el verano.
"Con muchas de estas herramientas e implementaciones", dijo Hayley Garnham, gerente de calidad de Van Dyke, "podemos asegurarnos de que allí mismo, en esa estación, cualquier problema que hayan tenido, está bien, se elimine para que la parte problemática no pueda solucionarse".pasarse adelante."
impresión 3D
También en Van Dyke y otras plantas, Ford está aprovechando la fabricación aditiva para herramientas de impresión 3D que los operadores pueden utilizar para facilitar sus trabajos y mantener las piezas organizadas y fácilmente accesibles.Esto ayuda a que los trabajos se realicen de manera consistente, con las piezas correctas y de manera más eficiente, dijo el gerente de planta, Mark Shkoukani.
Sólo la planta de Van Dyke tiene dos impresoras 3D grandes y una más pequeña, principalmente para prototipos que funcionan las 24 horas del día, dijo Bill Colwell, ingeniero líder de procesos.La impresión puede tardar entre 20 minutos y algunas horas, dependiendo del tamaño de la herramienta.Normalmente hay seis proyectos en cola y los trabajadores se acercan con ideas a diario.
Un empleado que trabaja en la línea puede acudir a Colwell o a uno de sus colegas cuando tenga una idea para una herramienta.Juntos, esbozarán un diseño, que Colwell usará para crear un diseño que la impresora 3D pueda producir, generalmente con plástico.El proceso puede poner una herramienta en manos de un operador en un día, en comparación con el pasado, cuando Ford tenía que recurrir a un proveedor, lo que podría llevar semanas o incluso meses si era necesario realizar más ajustes.
"Podemos implementar algo en unas pocas horas, probarlo y, si no funciona", dijo Colwell, "podemos regresar y tomar el mismo modelo que ya teníamos, imprimirlo de inmediato y simplemente hacer pequeños cambios".lo."
Chris Kipp, de 52 años, de Mount Clemens, líder del equipo de United Auto Workers en la planta de Van Dyke, colaboró con ingenieros para diseñar una herramienta que permite a los trabajadores colocar fácilmente en su lugar la tapa del extremo de un rotor, una pieza de una unidad motriz electrificada..Una herramienta que utilizaron originalmente requirió mucha fuerza para empujar el componente hacia abajo.
Kipp y los ingenieros descubrieron que al fabricar una herramienta que aprovecha el diámetro interior de la pieza en lugar del exterior, ofrecía una estabilidad que requería menos fuerza para colocar la tapa en su lugar.Como resultado, la tarea cuya duración variaba significativamente y podía tardar más de dos minutos en completarse se volvió menos variable y se realizó en menos de 80 segundos.
"Es mucho más fácil", dijo Kipp."Los operadores realmente lo sintieron en sus hombros".
Una mañana reciente, Tyler Amodeo, de 30 años, de Sterling Heights, ensamblador en la planta de Van Dyke, estaba usando múltiples herramientas 3D para realizar su trabajo.Un soporte para resortes ondulados le permitió agarrar rápidamente las arandelas grandes y delgadas sin que se enredaran.Puso varias piezas en un kit impreso en 3D que mantiene organizados los componentes en una plataforma mientras se envía a la línea del tren motriz.
"Me ayuda a ser organizado, eficiente y más rápido", dijo Amodeo.
Eso es clave, dijo Shkoukani, porque cuando los empleados no tienen las herramientas o piezas que necesitan, tienen que tomarse el tiempo para localizar la pieza correcta y asegurarse de obtener la correcta.
"Se eliminan un par de pasos", dijo."Cuando haces eso en varias estaciones en el futuro, simplemente haces los cálculos: son tantas veces. Es simplemente un gran ahorro".
entrenamiento de realidad aumentada
Río abajo, Dearborn Engine también ha implementado tecnología en un esfuerzo por producir resultados de calidad positivos al aumentar la capacitación de los empleados con Microsoft HoloLens, cuyo modelo de segunda generación se vende a partir de $3,500.
La planta ha incorporado gafas de realidad aumentada en su programa de formación junto con instrucciones escritas, observación de otra persona haciendo el trabajo y modelos 3D en pantalla.Un estudio colaborativo con el Instituto de Tecnología de Georgia demostró que el paso de realidad mixta ayudó con la memoria muscular, dijo el gerente de la planta, Nadeem Zaidi.
Eso es particularmente importante, porque si bien Ford tiene fortalezas como fabricante de gran volumen, dijo Zaidi, la planta de Dearborn ha agregado más líneas de sistemas de propulsión de nicho desde su reequipamiento cuando se relanzó la producción en 2021. Como resultado, se producen pocos motores en esas líneas.lo que significa que lleva más tiempo que el trabajo se convierta en algo natural.
La planta también está trabajando para capacitar a más empleados en trabajos que nunca han hecho, desde el ensamblaje hasta el mecanizado, dijo Zaidi, "Nos ayuda a distribuir la mano de obra de acuerdo con las personas que están presentes para trabajar".
La esperanza, dijo, es que HoloLens ayude a facilitar ese proceso.Al usar los auriculares, el alumno recibe instrucciones emergentes escritas paso a paso que pueden explicar cómo inspeccionar un motor F-150 Raptor R V-8, por ejemplo.Las líneas virtuales guían al usuario hacia dónde mirar, y el usuario puede seguir las instrucciones o permanecer quieto en un lugar determinado.
"La mayor ventaja, desde mi punto de vista, es que requiere un trabajo complicado y lo divide en pasos muy pequeños, y si sigues el proceso, llegarás al final", dijo Al Fisher, coordinador de lanzamiento."A veces un experto puede dar por sentado lo bueno que es. No hace eso. Te guiará metódicamente paso a paso".
Esto puede resultar útil en casos en los que la experiencia de un trabajador en un área es limitada.En un momento, la planta tenía un experto que podía inspeccionar cierto motor I-4 sin instrucciones.
"Si ese experto no está en la planta, entonces... estás como luchando para realizar las inspecciones", dijo Tim Mwenje, entrenador de Sistemas de Producción de Ford."Cuando te pones esto, incluso yo podría inspeccionarlo".
Más de 20 empleados de Dearborn Engine han sido capacitados utilizando HoloLens, y en julio Ford comenzó a rastrear el desempeño de un solo equipo donde cada miembro ha sido capacitado con la tecnología.Su aplicación se está expandiendo y explorando también en otras ubicaciones, incluida la planta de ensamblaje de camiones Dearborn, la planta de componentes Rawsonville en Ypsilanti y la planta de ensamblaje Louisville en Kentucky.
"Me gustaría que tuviéramos esto cuando yo tenía 18 años y recién comenzaba", dijo Reginald Bassett, de 42 años, de Redford Township, líder de equipo en Dearborn Engine."Soy una persona muy visual, así que es genial".
2024 detroitnews.com.Distribuido por Tribune Content Agency, LLC.
Citación:Cómo Ford utiliza la inteligencia artificial, la realidad aumentada y la impresión 3D para mejorar la calidad (11 de septiembre de 2024)recuperado el 11 de septiembre de 2024de https://techxplore.com/news/2024-09-ford-ai-augmented-reality-3d.html
Este documento está sujeto a derechos de autor.Aparte de cualquier trato justo con fines de estudio o investigación privados, noparte puede ser reproducida sin el permiso por escrito.El contenido se proporciona únicamente con fines informativos.