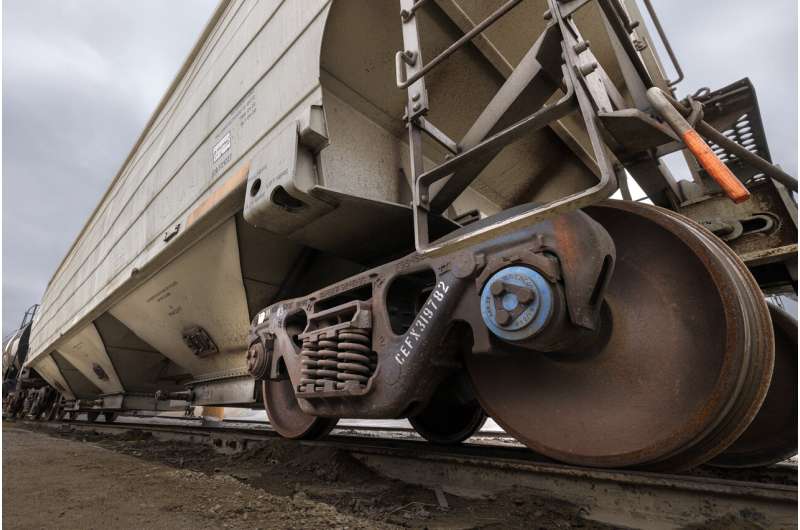
When Nebraska Engineering researchers began cooking up new recipes for manufacturing railcar bearing components, they expected there would be a few offerings that wouldn't be as satisfying.
However, rollers for a railroad tapered roller bearing produced using metal powders, a state-of-the-art 3D printing lab, and additive manufacturing processes proved to be just as robust as rollers made using currently conventional techniques.
Joseph Turner, Robert W. Brightfelt Professor of Mechanical Engineering, said the first-ever 3D-printed rollers for railroad bearings exceeded expectations, creating a starting point for expanding the use of this innovative process that could help to make transportation even safer. Their results were compiled into a paper—"Fatigue Performance of Bearing Rollers Manufactured by Laser Powder Bed Fusion"—that was published in Bearing and Transmission Steels Technology.
"We cooked up many different recipes and we printed many rollers," Turner said. "We expected the printed rollers to show failure early on in the tests, but the bottom line is they performed just as well as conventional rollers. Now, we're going to explore other ideas using this work as the foundation."
The team was led by Turner and recent mechanical engineering doctoral graduate Luz Sotelo. It also included former faculty member Michael Sealy, graduate students Cody Pratt, Guru Madireddy and Rakeshkumar Karunakaran, and industry partner Amsted Rail Brenco. The project also received support from the National Science Foundation and the Federal Railroad Administration. Sotelo was an NSF Graduate Fellow.
Turner said the team expected standard fatigue tests simulating the loads—up to 286,000 pounds per railcar over 250,000 miles traveled—would show the metal AM recipe for a printed bearing was in need of tweaking.
However, Turner said, the rollers printed in the College of Engineering's Nebraska Engineering Additive Technology Labs using 8620HC—a high-carbon steel—performed as well as those manufactured using current standard processes.
"Basically, when you look at the two types of rollers side by side, you can't see any difference in the look or their performance," Turner said. "A lot of times (in metal AM), you will have concerns about the porosity or the internal microstructure of the metals in the first printed objects. Our 3D-printed rollers held up to the demands of the loads and distance that are expected from the mass-produced bearings."
Typical railcar bearings have more than 40 rollers, which measure about 2 inches by ¾ of an inch, one bearing for each wheel, and a total of about 350 per railcar. The standard-use bearings, Turner said, are manufactured by cutting long loops of thick, steel wire into the required lengths and then grinding them down to create the tapers needed for optimal performance.
Using 3D printing to produce the rollers proved to be significantly more expensive than the current methods, Turner said. Despite that drawback, he said, the use of 3D printing could in the not-too-distant future find a place in many industries that use these types of bearings.
"You have to explore whether it's even possible before you can begin figuring out when it's cost effective," Turner said. "Setting up a production line that makes the bearings is a huge investment but, maybe, it can work in emergency situations—like a mining company in the outback of Australia has a failure that might otherwise hurt their ability to move their product. If they can 3D print a part and not have to wait for something to be shipped to them."
The next steps, Turner said, might also include looking at possible other ways to make 3D printing more financially sensible in the manufacturing process, such as using more expensive steel powders to create a coating on bearing components made from less expensive metals, to create an overall cheaper and more sturdy bearing with better properties.
"One of the things we in the NEAT Lab have become pretty proficient at is developing these new recipes for alloys," Turner said. "As prices for our ingredients and equipment continue to drop in price, we will be able to try rolling out some new things that could appeal to a lot of fields and industries."
More information: Luz D. Sotelo et al, Fatigue Performance of Bearing Rollers Manufactured by Laser Powder Bed Fusion, Bearing and Transmission Steels Technology (2024). DOI: 10.1520/STP164920220115
Citation: Researchers uncover ways to improve railcar roller bearing safety, strength (2024, April 15) retrieved 15 April 2024 from https://techxplore.com/news/2024-04-uncover-ways-railcar-roller-safety.html
This document is subject to copyright. Apart from any fair dealing for the purpose of private study or research, no part may be reproduced without the written permission. The content is provided for information purposes only.